
40+ YEARS OF EXPERIENCE
At AWC, we specialize in designing and manufacturing wire payoffs and decoilers for a wide variety of industrial applications.
Since our beginning, our goal has been to create innovative products that solve problems and streamline production for our clients. We’re proud to manufacture machinery known for excellent performance, durability, and cost-effectiveness.
Contact us today to learn more about our products or request a quote!

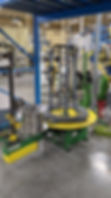
Precise Tension Control = Unmatched Energy Savings
We’ve put together our 40 years of building machines and 20 years of maintenance experience to bring you the energy-saving AWC Tension Control System. Providing constant tension on material for precise payoff, our Tension Control System is designed with innovative technology to lower your electrical consumption.
No clutches or brakes
The AWC Tension Control System features electronically-controlled speed, using less energy than our competitors’ products.
No abrupt starting and stopping
By providing smooth acceleration and deceleration, our Tension Control System avoids large energy usage spikes.
Explore more to learn how you can save energy and lower costs with AWC products!

The AWC Advantage
We're dedicated to making sure you get the best return on your investment when you purchase from us. Here are just a few ways our products stand out:
Durability
At AWC, all our equipment is load-tested and built to last. With at least 95% steel construction, our machines can withstand even the most heavy-duty applications.
Versatility
We provide machines in the widest range of available sizes, enabling our clients to handle virtually any type of material.
Energy Savings
Based on 20 years of maintenance experience plus 40 years of building machines. AWC's “Tension control system” provides constant tension on material for precise payoff.
No abrupt starting and stopping, which is a cost-saving option for your electrical consumption!
No clutches or brakes. Electronically controlled speed for smooth acceleration and deceleration, avoiding large energy requirements.
Longevity
AWC products are designed to last forever and need little maintenance. They are also designed to make repairs simple and quick when necessary.
Our Other Services
In-House Repairs
At AWC, we believe that selling you a product is only the beginning. If your unit needs repair down the line, we offer efficient in-house repairs.
Refurbished Products
Our refurbishment program is another way we can pass cost savings on to you, whether you want to buy a refurbished product or sell your used AWC machine. Get in touch today to learn more!